Gustave
Member
Hello Forum,
I am just about done designing a system to control my well pump. I've bought all the parts, but thought I might post my design here for any inputs before I implement it. There is still time to change things.
The details are as follows:
1. This is a shared well. Both my neighbor and I will use the same well.
2. I have a 10,000 gal cistern located 80 vertical feet above the well head. My neighbor has a 5,000 gal cistern located 140 vertical feet above the well head.
3. The linear distance from the well to the cisterns is roughly 700 ft in both instances.
4. I would like to be able to use water locally near the well head. Using the spigot on the manifold. Hence the pressure switch.
5. I originally planned to use solenoid valves to control the flow to the two cistern tanks. But I became concerned that they would work reliably with the residual pressure from all that elevation. So I switched to motorized ball valves. They take about 40 seconds to open or close and are powered by 230 V AC
6. I have a 1000 ft roll of 2-conductor 14 GA wire that I plan to use (inside a conduit) to allow the float switches inside the cistern tanks to turn on the pump. The original plan was to just open the motorized valves and let the pressure switch turn on the pump. But 140 ft of elevation equates to 60 psi of residual pressure. I was not sure a pressure switch would work for that.
7. The plan is to run 230V AC from the pump controller to the float switches and back. Since the current should be minimal, voltage losses should not be an issue. I think (hope?).
8. I plan to implement a pump saver and a cycle stop valve. Not sure if they are both necessary. The CSV is mostly when water is used local to the well head without a cistern.
Here is a sketch of my proposed system. If anyone has any comments I would be happy to hear them. Thank you. Gustave
I am just about done designing a system to control my well pump. I've bought all the parts, but thought I might post my design here for any inputs before I implement it. There is still time to change things.
The details are as follows:
1. This is a shared well. Both my neighbor and I will use the same well.
2. I have a 10,000 gal cistern located 80 vertical feet above the well head. My neighbor has a 5,000 gal cistern located 140 vertical feet above the well head.
3. The linear distance from the well to the cisterns is roughly 700 ft in both instances.
4. I would like to be able to use water locally near the well head. Using the spigot on the manifold. Hence the pressure switch.
5. I originally planned to use solenoid valves to control the flow to the two cistern tanks. But I became concerned that they would work reliably with the residual pressure from all that elevation. So I switched to motorized ball valves. They take about 40 seconds to open or close and are powered by 230 V AC
6. I have a 1000 ft roll of 2-conductor 14 GA wire that I plan to use (inside a conduit) to allow the float switches inside the cistern tanks to turn on the pump. The original plan was to just open the motorized valves and let the pressure switch turn on the pump. But 140 ft of elevation equates to 60 psi of residual pressure. I was not sure a pressure switch would work for that.
7. The plan is to run 230V AC from the pump controller to the float switches and back. Since the current should be minimal, voltage losses should not be an issue. I think (hope?).
8. I plan to implement a pump saver and a cycle stop valve. Not sure if they are both necessary. The CSV is mostly when water is used local to the well head without a cistern.
Here is a sketch of my proposed system. If anyone has any comments I would be happy to hear them. Thank you. Gustave
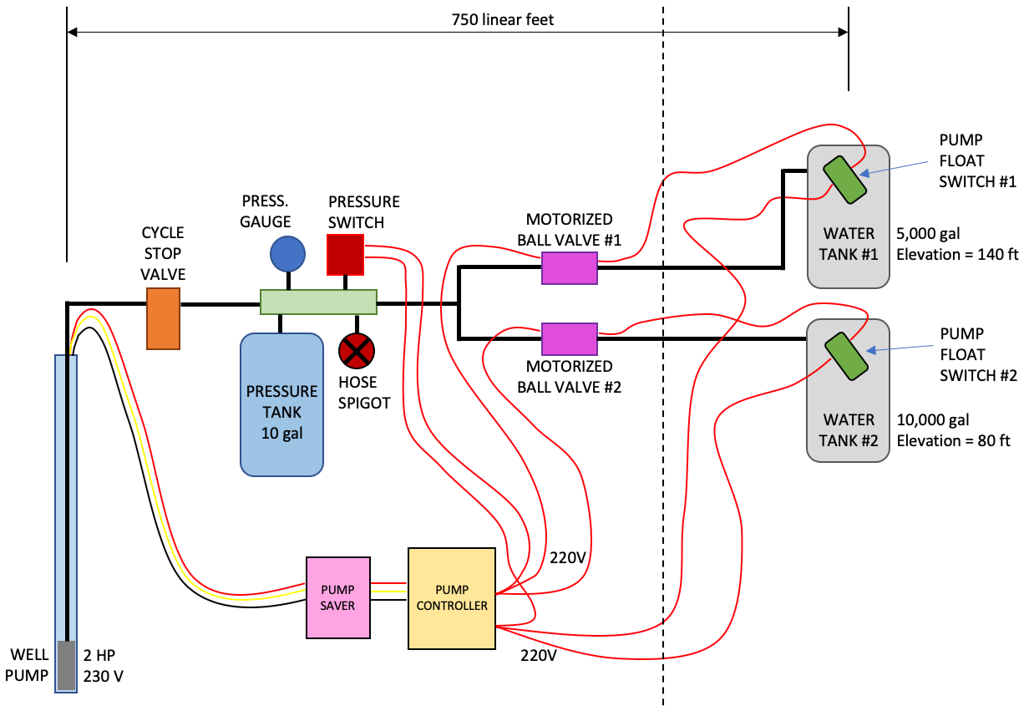